Auf vielfachen Wunsch gibt es von mir jetzt mal ein kleines Tutorial zum Abformen von Teilen mit Silikon und dem anschließenden Gießen mit Resin.
In diesem Tutorial geht es um einteilige Silikonformen.
Die Bilderstrecke zeigt mein grundsätzliches Vorgehen.
Nach einigen Jahren mit unzähligen Tests und literweise misslungenem Resin und Silikon, erziele ich damit die besten Ergebnisse.
Ich nutze dabei Maschinen, die sicher nicht jeder im Hobbykeller stehen hat.
Grundsätzlich geht es zwar auch ohne, aber die Ergebnisse sind dann ggf. nicht ganz so gut und/oder nur aufwendiger zu erreichen.
Schalung bauen
Ich beginne zunächst mit dem Bau der Schalung zum Abformen des Masters.
Als Schalung nutze ich die unterschiedlichsten Materialien.
Plastikbecher, wenn es rund werden soll und beschichtete Pappe, Polystyrolplatten oder Forexplatten wenn eine Kastenform erforderlich ist.
Die Bodenplatte beklebe ich mit dünnem doppelseitigem Klebeband.
Darauf wird der Master dann fixiert.
Die Wände der Schalung klebe ich dann meist von außen mit Heißkleber fest.
Achtung! Das Silikon verträgt sich nicht mit jeder Sorte doppelseitigem Klebeband.
Insbesondere mit Sekundenkleber verträgt sich das Silikon überhaupt nicht gut!
Die Wandstärke der Silikonform richtet sich nach der Größe und Gestalt des Bauteils und wie viele Kopien man machen möchte.
Generell muss die Form, das flüssige Resin stützen können ohne sich zu verformen. Möchte man Teile mit größerer Masse und/oder in größerer Stückzahl kopieren, empfielt es sich die Wandstärken zu erhöhen.
Über den Daumen sollte man aber ca. 1 cm Wandstärke nicht unterschreiten.
Wenn der Master aus Kunststoff, Resin, Spachtel- oder Modelliermasse besteht (also nicht saugfähigen Materialien) ist ein Trennmittel nicht nötig.
Der Selbsttrenneffekt des Silikons sorgt dafür, dass sich der Master leicht aus der Silikonform lösen lässt.
!Vorsicht! bei nicht vorbehandeltem FED, FUD und WSF Material von Shapeways.
Meist lies sich das Silikon nicht ohne Beschädigungen davon lösen!
Ich empfehle bei diesen Materialien, vorher zu grundieren oder sogar mit glänzender Farbe zu lackieren!
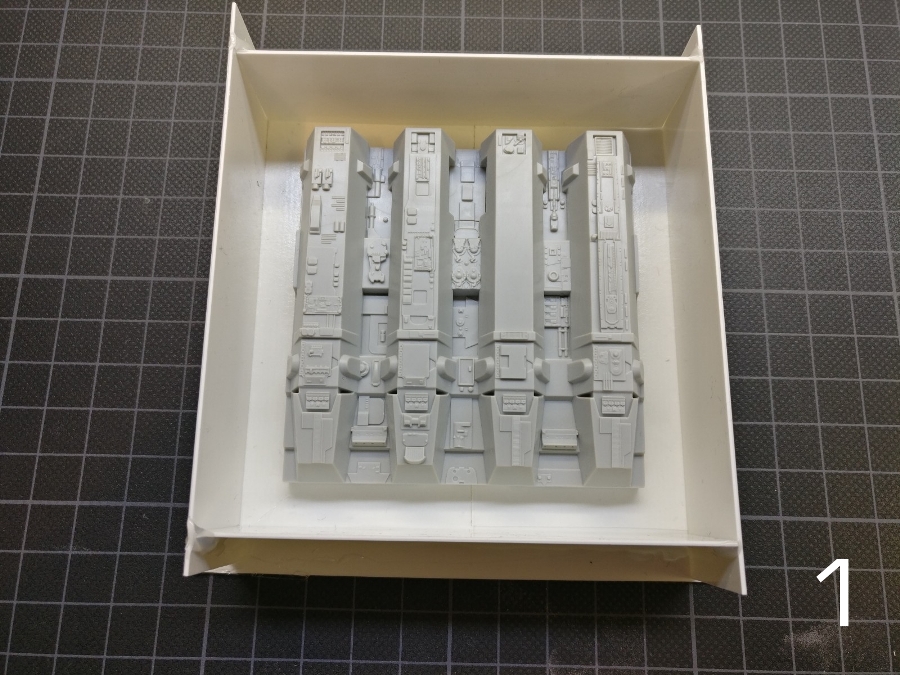
Bauteil in der Schalung aus Polystyrolplatten
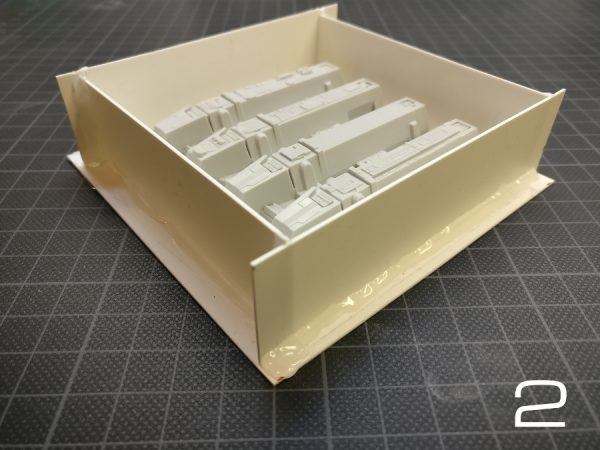
Verklebt mit Heißkleber
Silikon Anmischen
Ist die Schalung fertig gestellt, wird eine kleinere Menge Silikon angemischt.
Ich nutze Typ 1 (grün/weiß) von Trollfactory.
Das Mischungsverhältnis von 1/1 sollte sehr exakt eingehalten werden (auch und besonders bei sehr kleinen Mengen).
Andernfalls kann es passieren, dass das Silikon nicht fest wird und sehr aufwendig vom Master entfernt werden muss!
Nach dem Mischen befinden sich sehr viele sichtbare und noch mehr nicht sichtbare Luftblasen in der Mischung.
Idealerweise sollte die Mischung jedoch blasenfrei sein.
Wer keine Vakuumkammer, oder wie ich, eine Vakuummischanlage zur Verfügung hat, sollte bereits beim Anmischen der Komponenten ein Einrühren von Luft vermeiden.
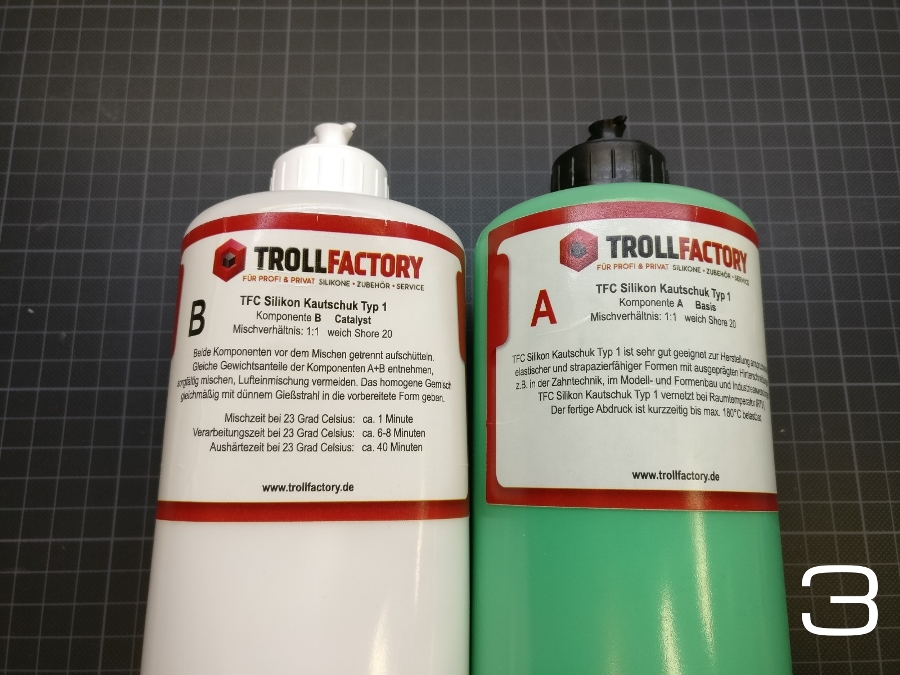
Silikon Typ 1 von Trollfactory
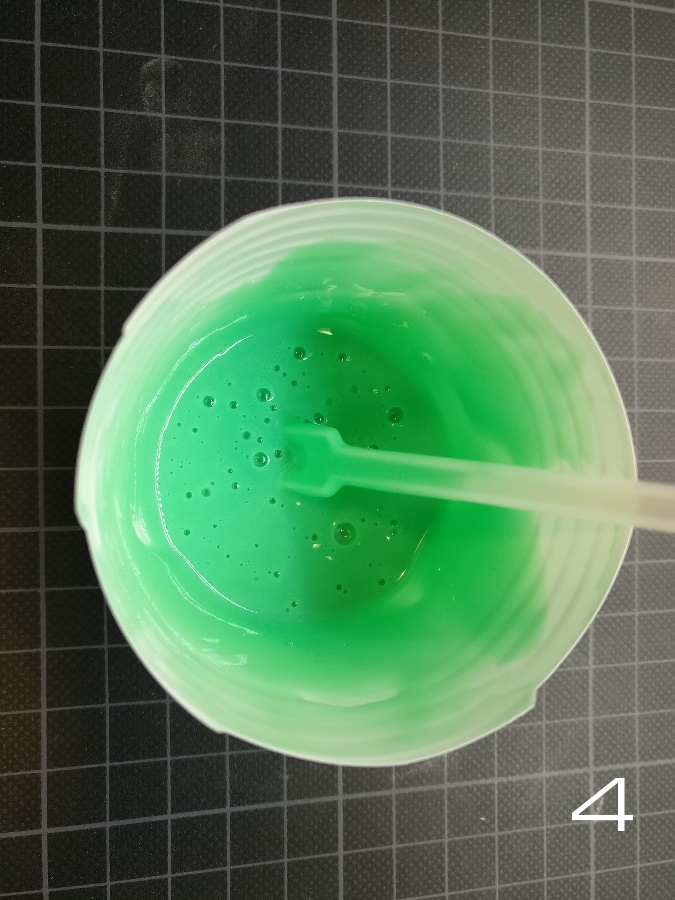
Silikon gemischt, aber noch nicht entlüftet
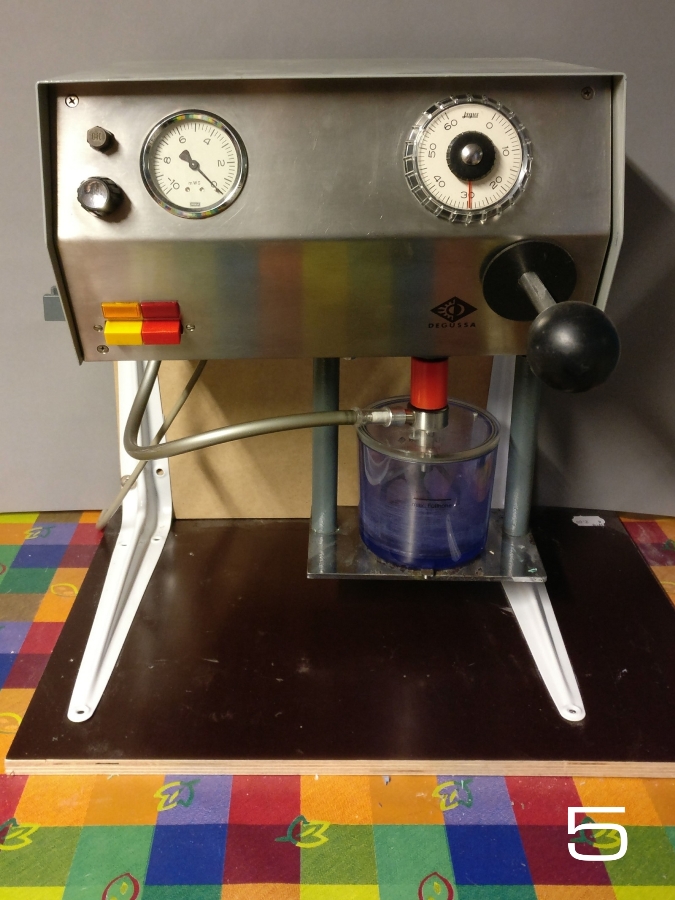
Vakuummischanlage
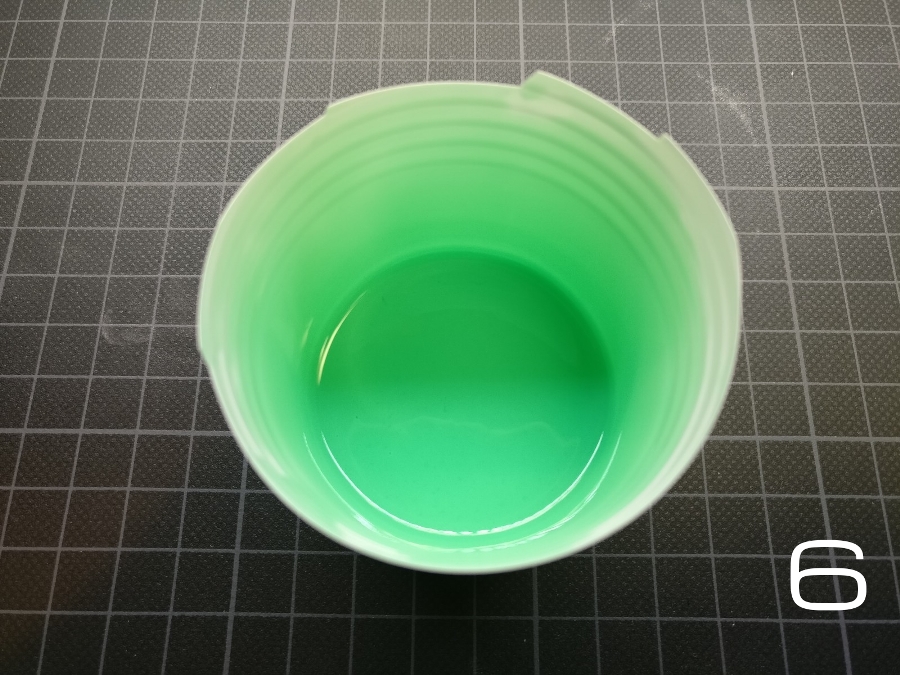
Keine Luftblasen mehr nach dem Entlüften
Oberflächen vorbehandeln
Damit die Oberfläche des abzuformenden Teils möglichst perfekt abgeformt wird und sich keine oberflächennahen Luftblasen im Silikon befinden,
betupfe ich sie zunächst mit einem zurecht geschnittenem Küchenschwamm (die ganz billigen).
Eine hauchdünne Schicht Silikon auf der Oberfläche des Masters erlaubt es Luftblasen, leicht zu entweichen.
Diese Schicht lasse ich min. 30 Minuten antrocknen (abdecken wegen Staub!)
Anschließend wird weiteres Silikon angemischt um die Form ganz aufzufüllen.
Durch richtiges Befüllen, lassen sich Luftblasen stark reduzieren.
Hier ein paar Tipps:
1. Schalung möglichst schräg halten
2. Schalung am tiefsten Punkt und nur an einer Stelle befüllen (am besten am Rand neben dem Master). Also nicht über das Bauteil kippen, wie ich es oft sehe.
3. Das Silikon möglichst langsam am Bauteil aufsteigen lassen, damit Luft aus Vertiefungen und Details nach oben entweichen kann und nicht eingeschlossen wird.
4. Das Silikon aus möglichst großer Höhe in einem möglichst dünnen Strahl fließen lassen.
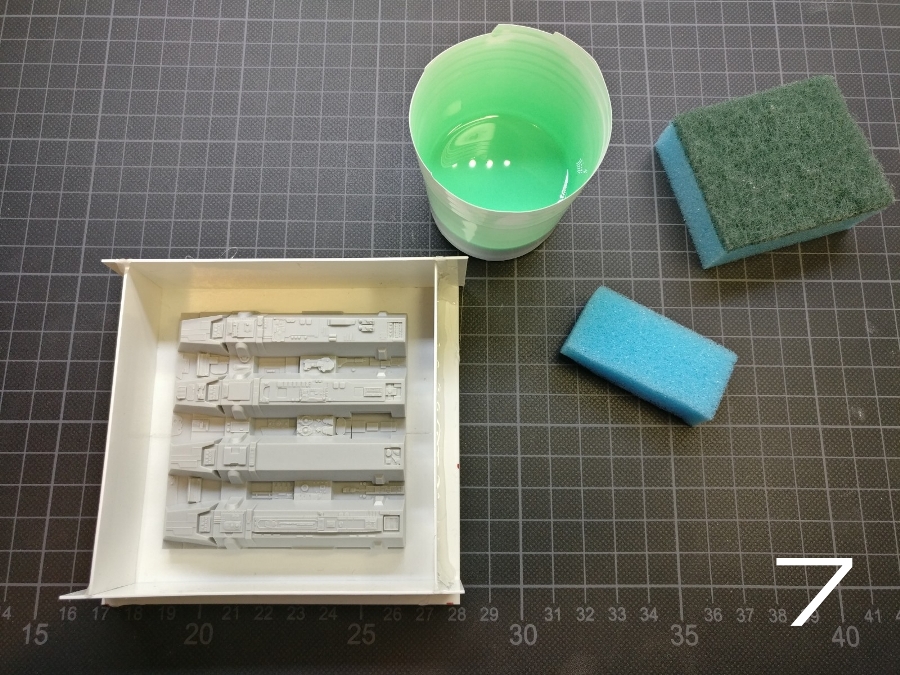
Küchenschwamm zum Tupfen
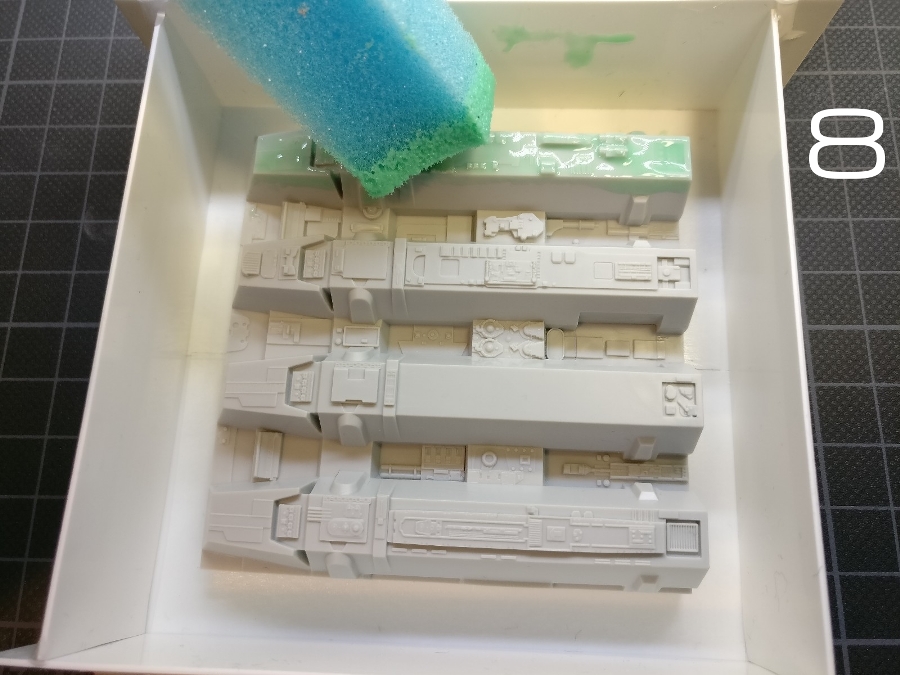
Betupfen der Oberfläche
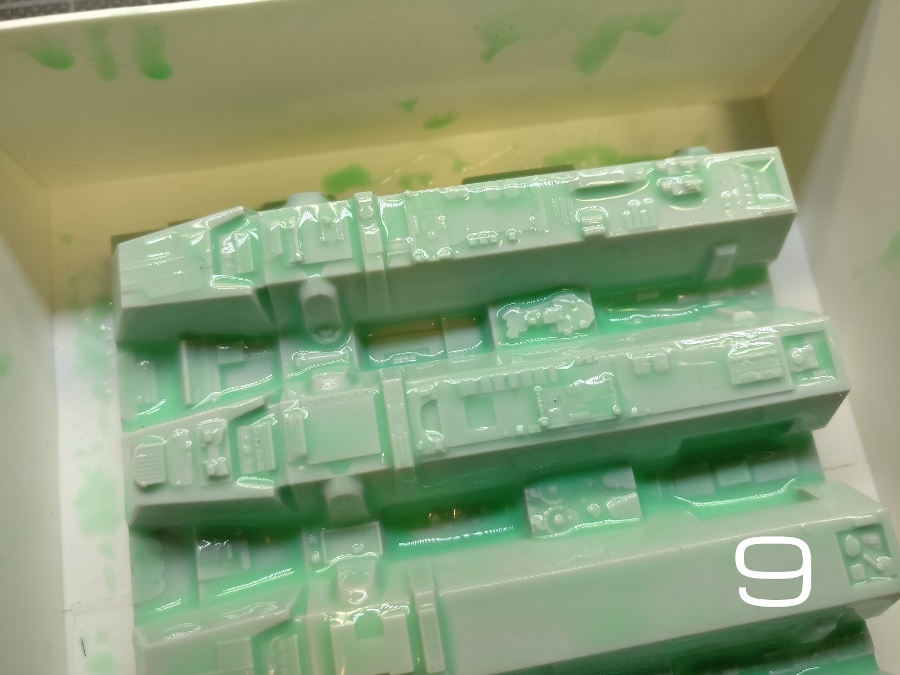
Eine Sehr dünne Schicht Silikon auf der Oberfläche
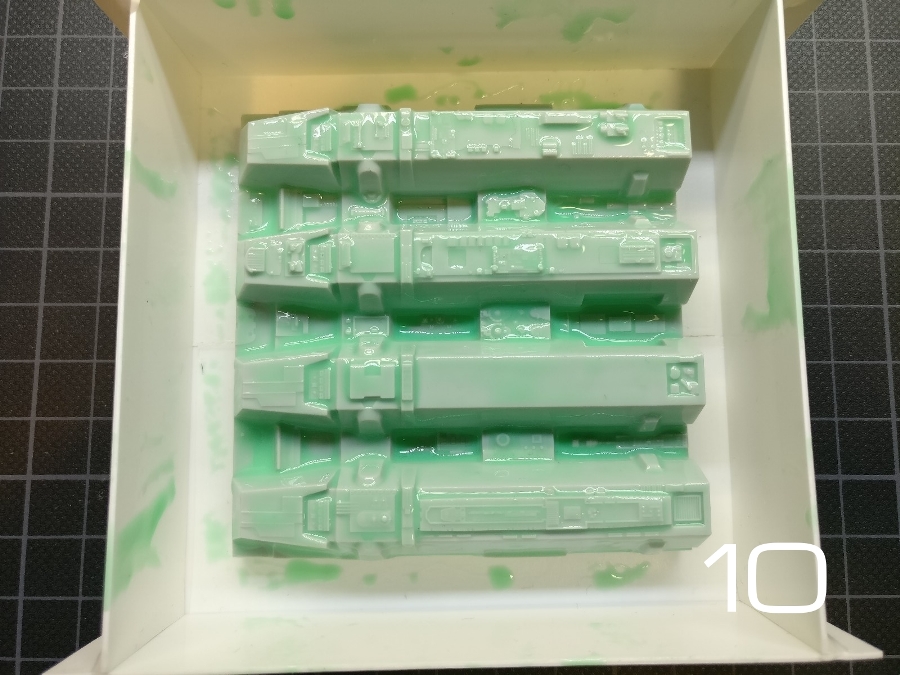
Silikon nach dem Erhärten
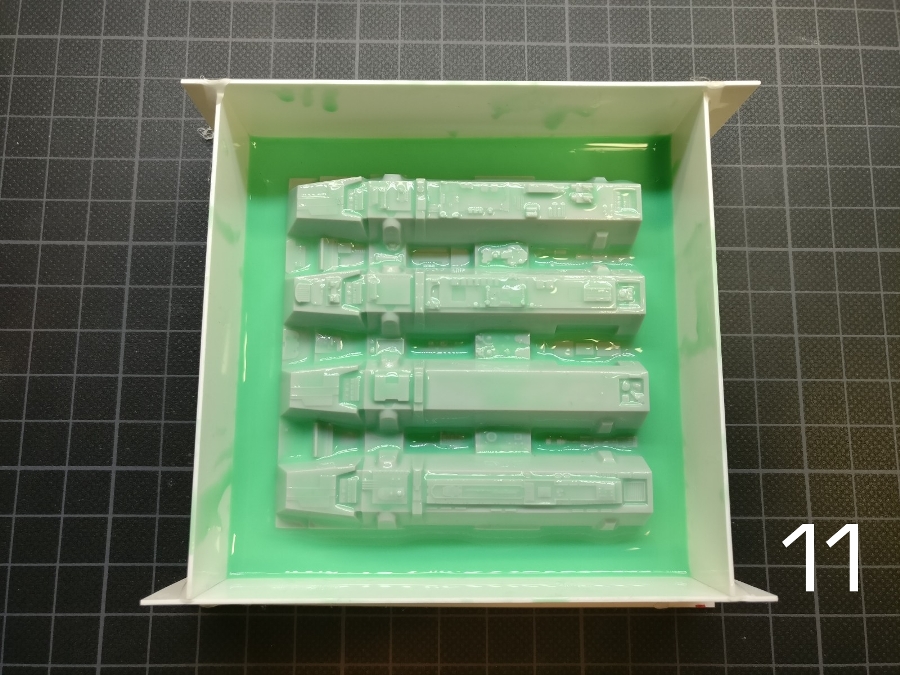
Auffüllen der Form
Silikonform nacharbeiten
Nachdem das Silikon ausgehärtet ist, kann es aus der Schalung entfernt und der Master entnommen werden.
Man sollte alle Kanten der Silikonform, vor allem die Unteren, mit der Schere beschneiden.
Die Kanten stehen vom Gießen des Silikons leicht hoch.
Dadurch liegt es beim Resingießen nicht flach auf und das Gussteil verformt sich.
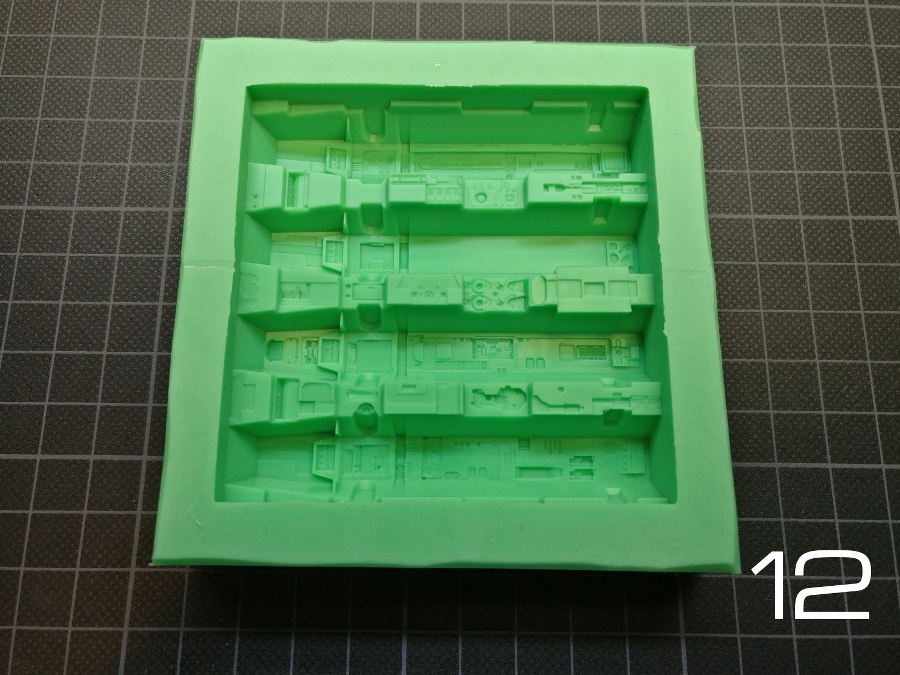
Die Silikonform nach der Entnahme aus der Schalung
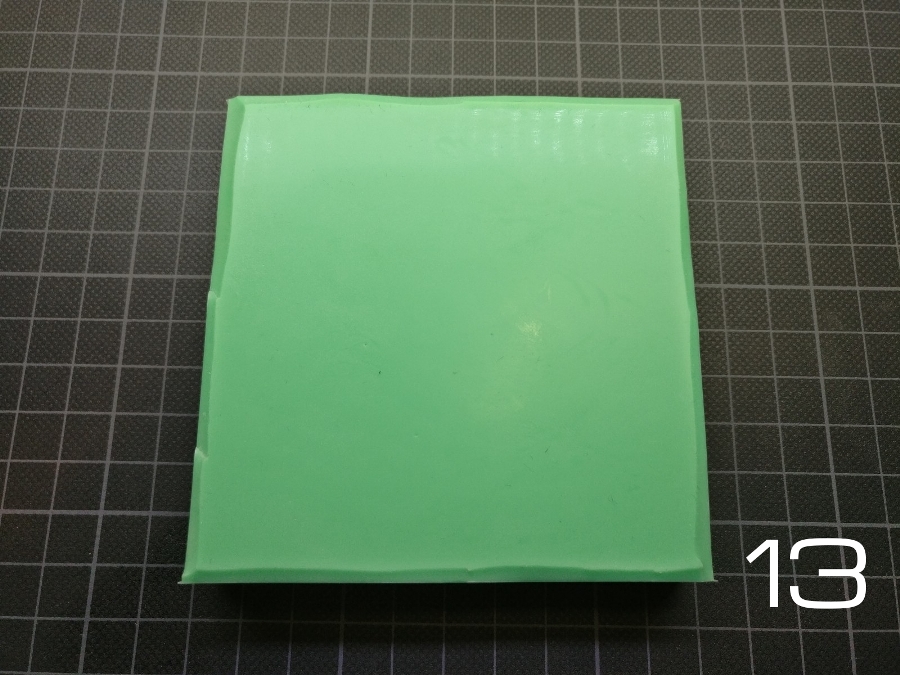
Silikonform mit beschnittenen Kanten
Silikonform zum Guss vorbereiten
Aus mehreren Gründen benutze ich kein flüssiges Trennmittel für die Silikonform.
Ich benutze Babypuder vor jedem Befüllen der Silikonform.
Auspudern, dann mit einem Kosmetikpinsel auspinseln und anschließend die Reste aus den Details blasen.
Puder hat neben der sehr guten Trennwirkung folgende Vorteile gegenüber flüssigen Trennmitteln:
1. Man muss die Resinteile anschließend nicht abwaschen bevor man sie lackieren kann.
2. Das Puder bricht die Oberflächenspannung des Resins und es fließt besser in Details
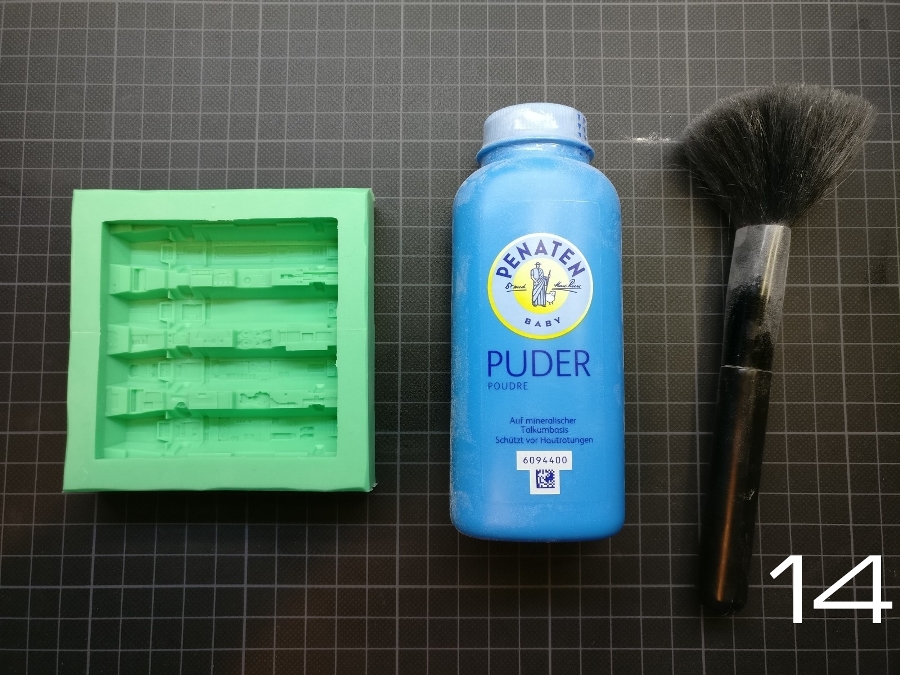
Babypuder und Kosmetikpinsel
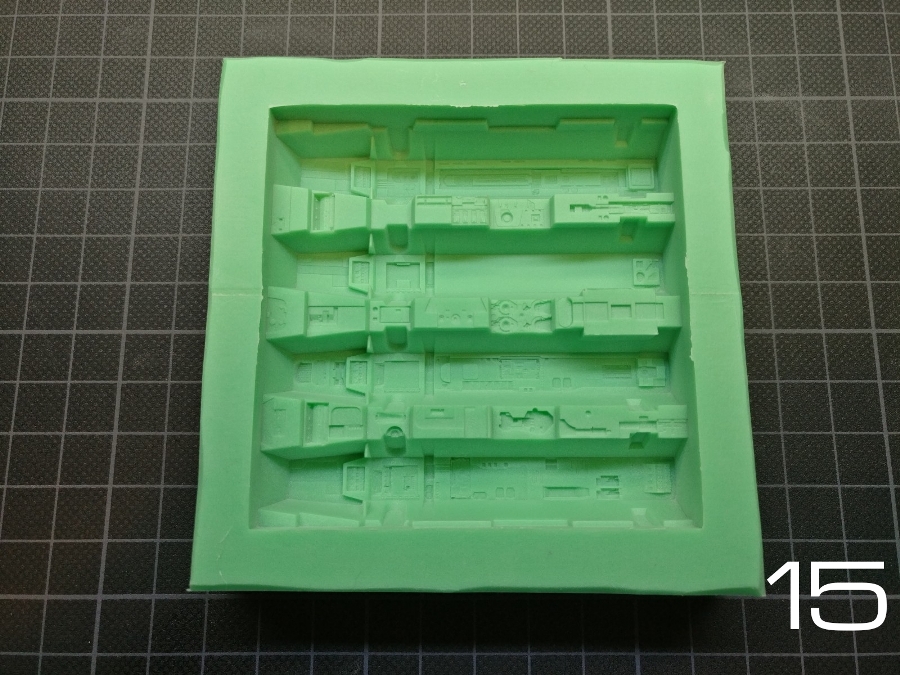
Ausgepuderte Form
Resin anmischen
Für das Anmischen des Resins gilt ebenfalls, möglichst wenige Luftblasen einmischen!
Jenachdem welches Resin man nutzt, sollte auch hier auf das Mischungsverhältnis geachtet werden.
Zu viel Härter = Mischung wird schneller hart
Zu wenig Härter = Mischung wird langsamer hart oder bleibt gummiartig
Resinkomponenten warm gelagert = Mischung wird schneller hart
Resinkomponenten kalt gelagert = Mischung wird langsamer hart
Generell gilt: Je größer die angemischte Menge Resin ist, umso schneller wird sie hart!
Die vom Hersteller angegebenen Topfzeiten und Aushärtezeiten gelten meist für eine Standardmenge von 100g.
Zum Beispiel kann ein Resin mit 4 Minuten Topfzeit und 45 Minuten Aushärtezeit bei einem sehr kleinen Bauteil (5g)
erst nach 2 Stunden fest sein, wohingegen ein 500g Bauteil bereits nach 20 Minuten fest ist.
Entsprechend variieren auch die Topfzeiten.
Man sollte generell zügig anmischen und gießen, denn je flüssiger das Resin ist, umso besser fließt es in Details der Form.
Resin gießen
Für das Einfüllen des Resins in die Silikonform gilt grundsätzlich das Gleiche wie für das Silikon (bis auf das Einfüllen aus großer Höhe).
Man sollte immer versuchen so zu gießen, dass Luftblasen aus Details entweichen können und nicht eingschlossen werden.
Wenn eine Druckkammer zur Verfügung steht muss man sich zur Einfülltechnik weniger Gedanken machen.
Luftblasen werden unter Druck (3 bar) an jeder Stelle eliminiert (zusammen gedrückt). Sollte keine Druckkammer vorhanden sein, empfehle ich bei Bauteilen mit vielen feinen Details (wie beim Silikon) die Oberfläche zunächst mit Resin abzutupfen oder auszupinseln und nach dem Erhärten weiter auszugießen.
Je nach Resinsorte muss man ein gewisses Schrumpfen während des Erhärtens einplanen.
Füllt man die Form randvoll, wird nach dem Erhärten ggf. eine Mulde entstanden sein, die man nachträglich ausgießen muss.
Das kann schwierig werden, wenn die Vertiefung nur sehr flach ist.
Oft empfielt es sich, bereits im Voraus zwei Gussschritte einzuplanen und die Form beim ersten mal nur 3/4 oder 4/5 zu befüllen.
Nach dem Aushärten des Resins, kann das Bauteil entnommen werden und wir sind fertig.
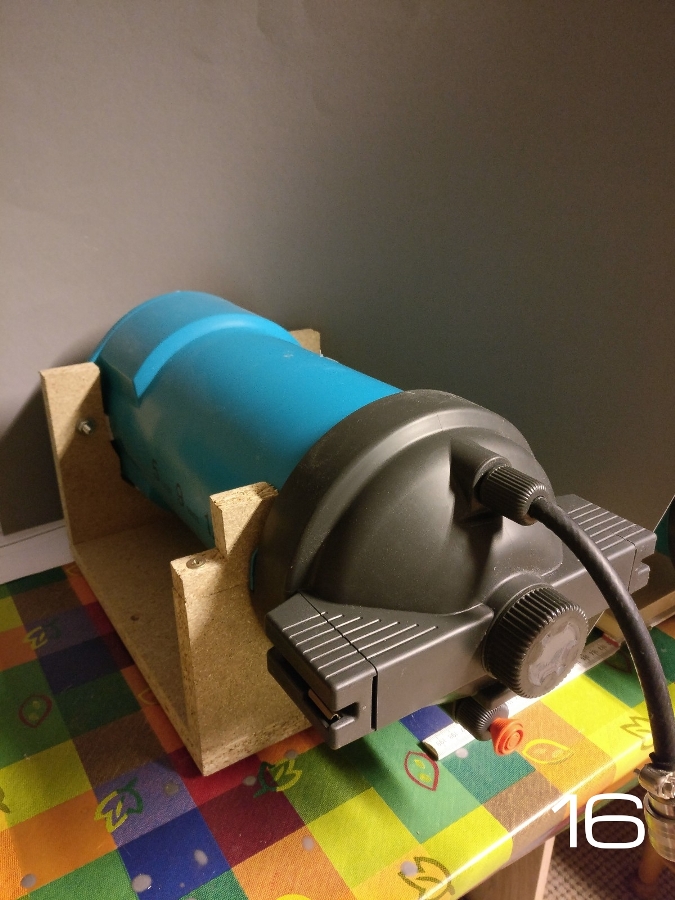
Kleiner Druckbehälter
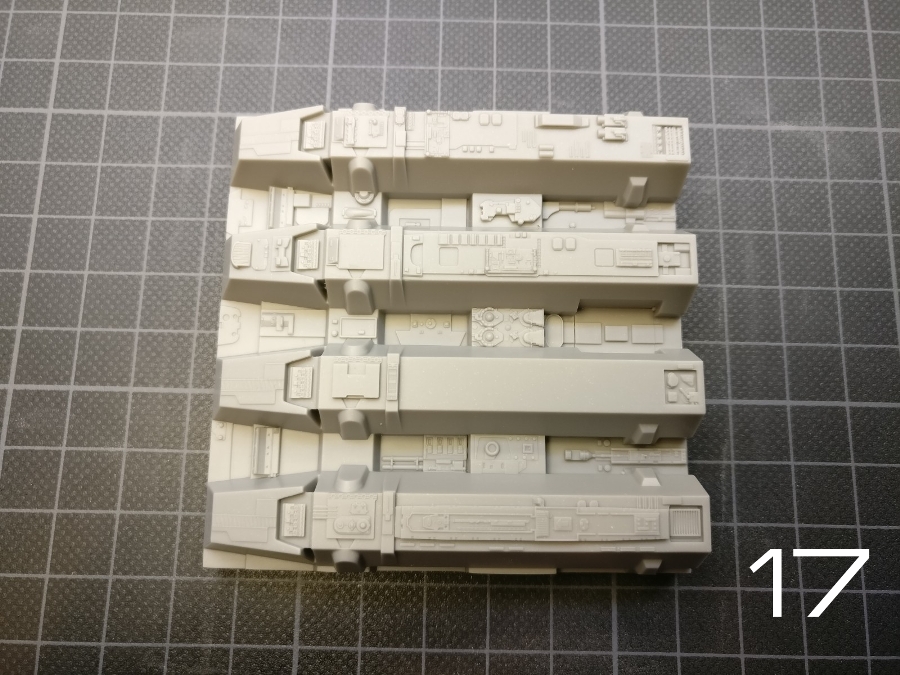
Fertig gegossenes Teil
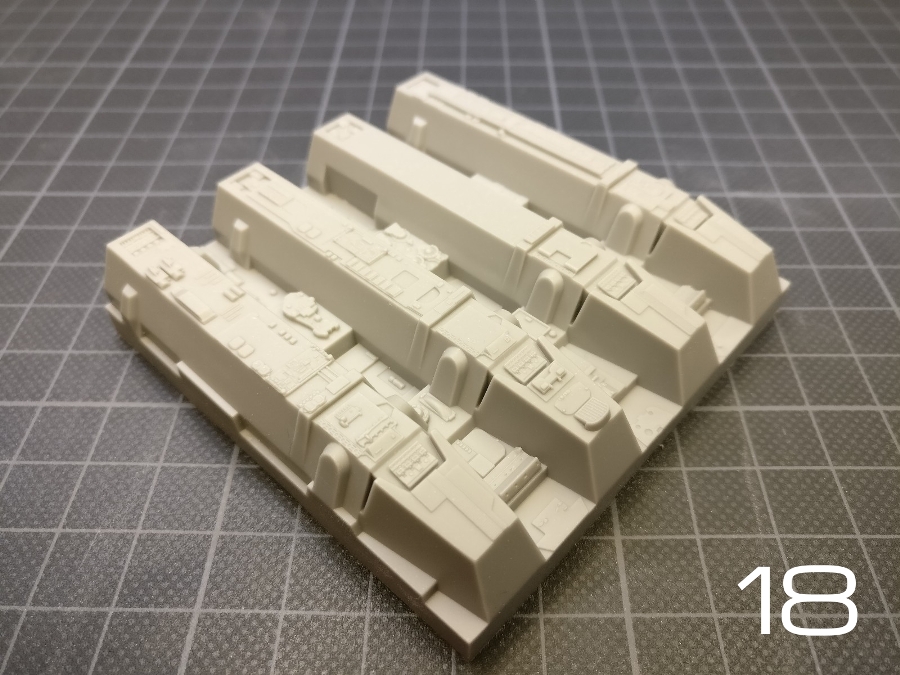
Fertig gegossenes Teil
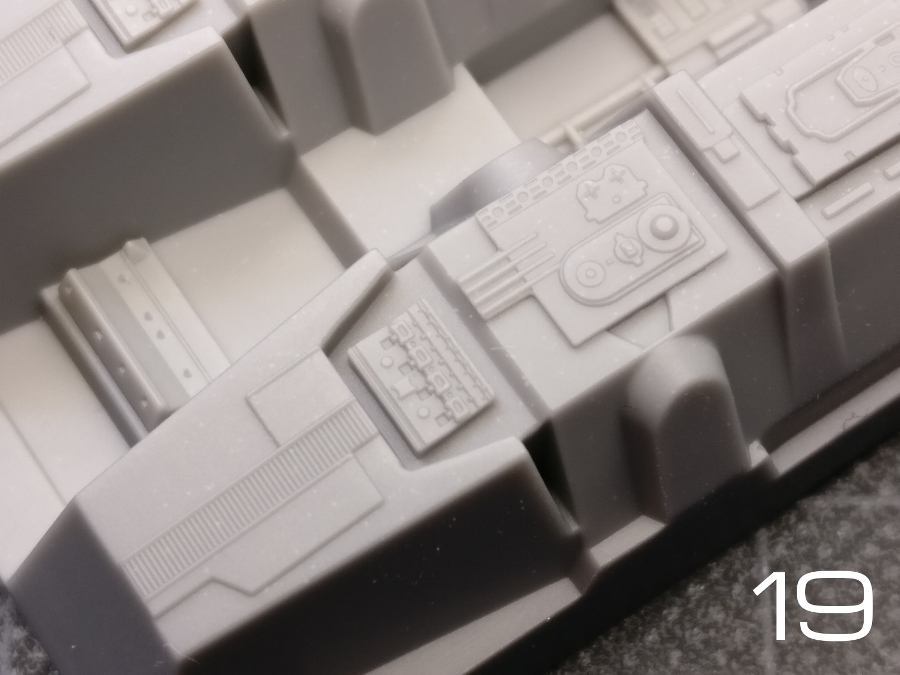
Details
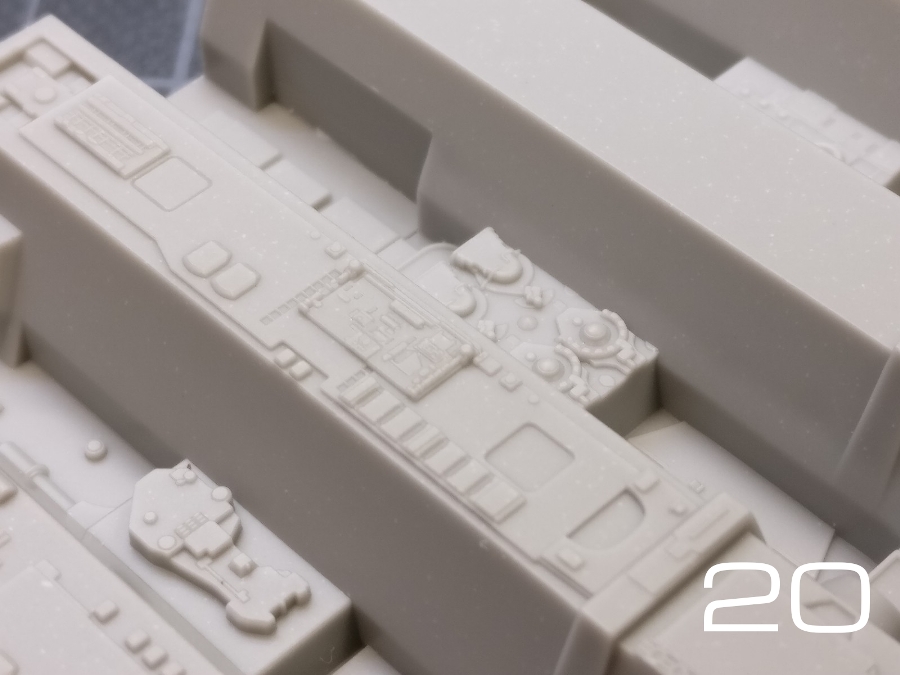
Details
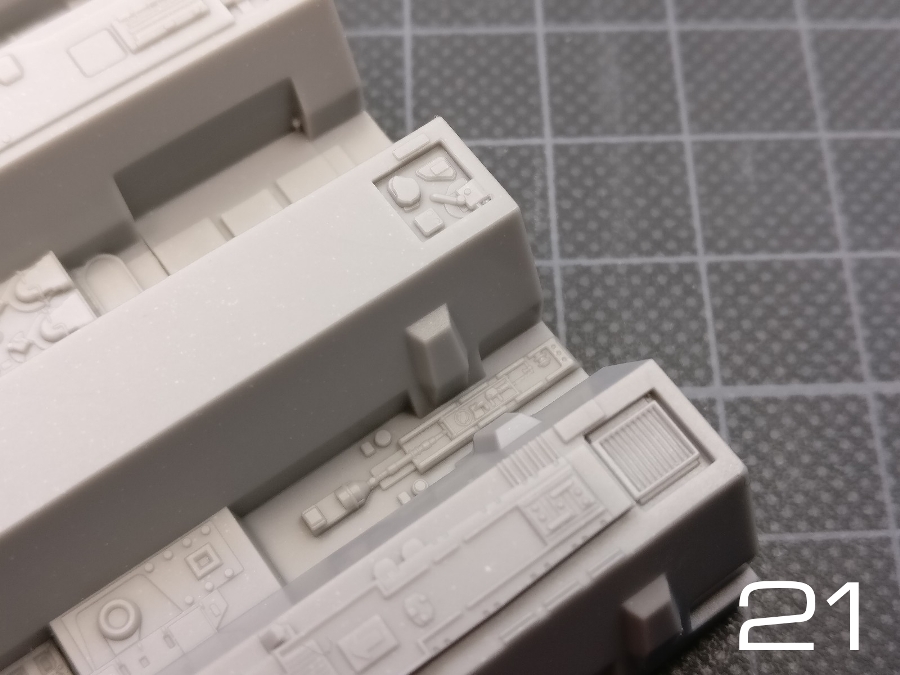
Details
An dieser Stelle endet mein kleines Tutorial zum Abformen und Gießen von einfacheren Bauteilen erstmal.
Beim nächsten Mal erläutere ich das Vorgehen zur Erstellung von zweiteiligen, anspruchsvolleren Formen.